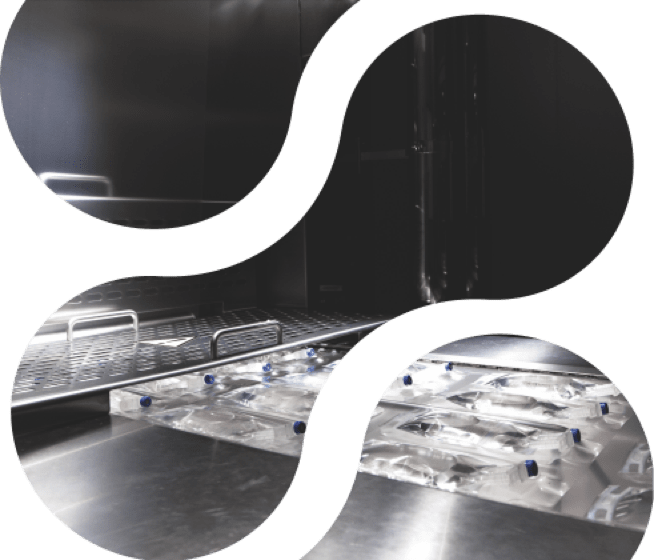
Form-Fill-Seal (FFS)
We develop and manufacture our own flexible bags on site ensuring a perfect match between the drug and its container. This model enables us to control the entire process from start to finish, helping to ensure the highest quality standards for our customers.
We operate eight fully automated Form-fill-seal (FFS) lines designed for 50 mL, 100 mL, 250 mL, 500 mL, and 1000 mL polypropylene bags, with the flexibility to accommodate custom sizes. Form-fill-seal optimizes drug manufacturing costs, reduces lead times, and enhances patient safety.
Filling and packaging occur within controlled clean room conditions, minimizing human intervention, contamination risks, errors, and maximizing quality assurance.
Form Fill Seal Manufacturing Line
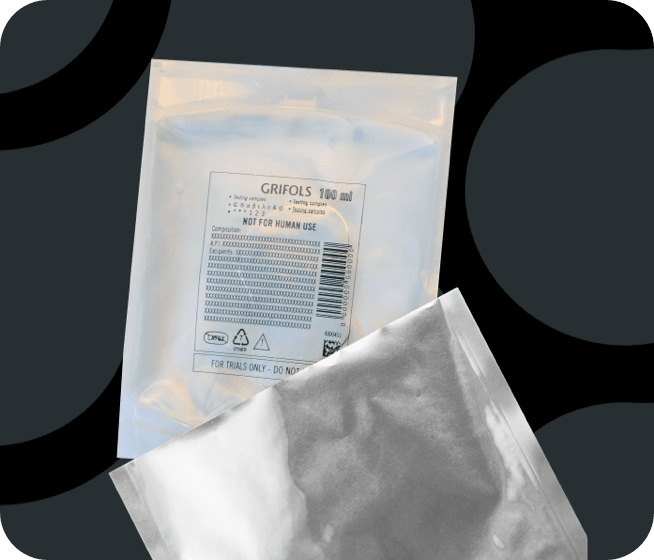
Oxygen and Light Sensitive Products
We manufacture parenteral preparations containing one or more active ingredients, intended for administration by injection, or infusion. These can be packaged in different high barrier materials (opaque aluminum and transparent high barrier overwrapping) to protect from oxygen and light.
Artificial Vision for Particle-Free Solutions
Ensuring particle-free solutions is crucial, so in addition to human visual inspection, we've incorporated artificial vision equipment to detect particle presence.
One major source of particle generation is the bag molding process so we have integrated this process into our filling operations by adopting form-fill-seal technology to maintain control over this critical aspect of injectable solution manufacturing.
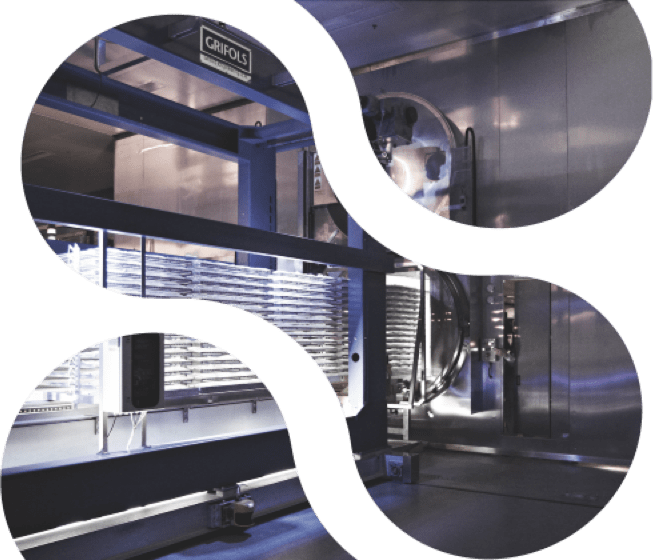
Terminal Sterilization
All manufacturing lines at our two sites are designed to fill finished sterile solutions with terminal sterilization in high-capacity autoclaves (water and steam).